Plate and Frame Filter Press
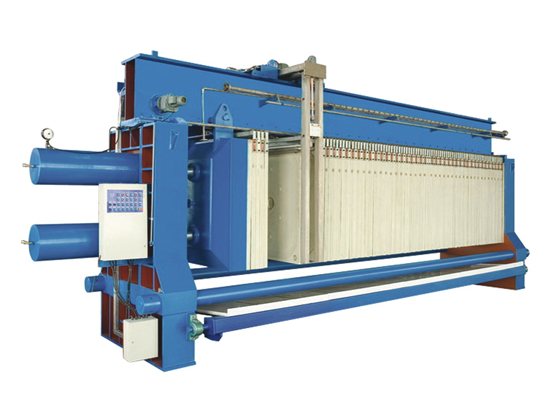
Plate and Frame Filter Press
Filter presses were introduced at the turn of the century and have been around for many years. A filter press contains a series of plates with a filtering surface on both sides. The plates are covered with a press cloth. Many of these plates are pushed together to form chambers with sufficient filtration area for the application. A slurry is forced into the chamber. The press cloth allows the filtrate to pass through, dewatering the filter cake which forms on the press cloth. The cake is discharged by pulling the plates apart. The cycle then repeats itself. Filter presses are among the most versatile of all liquid/solid separation unit operations. They adapt easily to variations in feed concentrations, particle size and other physical properties, delivering very dry cake and high solids capture with low chemical conditioning costs.
Press Types:
- Plate and frame
- Recessed chamber
- Membrane chamber
Typical Applications:
- Silicas / Silicates
- Pigment and dyes
- Chemical processing
Menardi manufactures all styles of press cloths including drape-over, cgr, and cloths with connecting sleeves. We provide head, tail, and intermediate press cloths in various medias and designs including plain cloths, and center and corner feed holes. We also offer backing cloths in many different styles and configurations.
Technical Feature
Sludge treatment
A volume reduction of approximately 30 – 80 % can be reached with sludge thickening before a further treatment. At smaller wastewater treatment plants, where the sludge is driven off regularly, thickening usually takes place directly in the sludge storage tank. The sludge is compressed at the tank bottom only by the force of gravity, while above the sludge a cloudy water layer is formed, which is taken off and led back into the inlet.
On larger plants separate thickening basins exist. These basins are equipped with slow rotating vertical rods, which create micro canals in the sludge for a better dewatering. Also pure machine thickening is gaining more significance with e.g. non-stabilised sludges, that could rot during the storage.
Working fast, precise, quiet and and long cutting life.
High percent of cobalt Working fast, precise, quiet and safe.
Reducing cutting time. Segment size and performance parameters
Precise segment size.
High grade of diamonds .
Product performance
-
The filter press is suitable for almost all types of sludge:
- Hydrophilic organic sludge: inorganic conditioning is often recommended to enable satisfactory cake release due to minimal aderence to filter cloth.
- Hydrophilic inorganic sludge: the filer press generally requires the addition of lime only.
- Hydrophobic inorganic sludge: it is very dense and ideal for the filter press. It is dewatered without any preliminary conditioning.
- Oily sludge: the filter press can be used to treat sludge containing light oils, the presence of grease can sometimes impair the smooth running of the filter; clothes have to be degreased at frequent intervals.